Introduction
Diesel generators play a crucial role in providing backup power in various industries, ensuring continuity during power outages or in remote locations where grid power is unavailable. However, the efficient operation of diesel generators is essential to minimize fuel consumption, reduce maintenance costs, and extend equipment lifespan. Monitoring the performance and efficiency of diesel generators is key to achieving these objectives. In this article, we will explore the importance of efficiency monitoring for diesel generators, the key parameters to measure, the available monitoring technologies, and best practices for optimizing generator performance.
Importance of Efficiency Monitoring
Efficiency monitoring of diesel generators is essential for several reasons, including:
1. Cost Savings: By monitoring the efficiency of a diesel generator, operators can identify inefficiencies and take corrective actions to optimize fuel consumption. This can result in significant cost savings over the long term, especially for generators that run continuously or for extended periods.
2. Maintenance Planning: Monitoring key performance parameters of diesel generators can help predict potential issues before they escalate into costly breakdowns. By detecting anomalies early, maintenance schedules can be optimized, reducing downtime and preventing unexpected failures.
3. Environmental Impact: Diesel generators are a significant source of emissions, including greenhouse gases and particulate matter. Monitoring efficiency can help operators reduce fuel consumption and emissions, contributing to a cleaner environment and compliance with regulations.
4. Equipment Longevity: Efficient operation of diesel generators can help extend the lifespan of the equipment. By monitoring performance parameters and addressing issues promptly, operators can prevent premature wear and tear, leading to increased reliability and durability.
Key Parameters for Monitoring
To effectively monitor the efficiency of diesel generators, operators need to track several key parameters that influence performance. Some of the critical parameters to monitor include:
1. Fuel Consumption: Measuring fuel consumption is essential for assessing the efficiency of a diesel generator. By tracking fuel usage over time and comparing it with the power output, operators can calculate the generator's fuel efficiency and identify opportunities for improvement.
2. Load Profile: Monitoring the load profile of a diesel generator helps operators understand how the generator is utilized and whether it operates within its optimal range. By adjusting the load profile to match the generator's capacity, fuel consumption can be optimized, and wear on the equipment can be minimized.
3. Temperature and Pressure: Monitoring the temperature and pressure of key components, such as the engine, coolant, and lubrication system, is crucial for detecting potential issues related to overheating or inadequate lubrication. Deviations from normal operating conditions can indicate underlying problems that require attention.
4. Emissions: Monitoring emissions, such as nitrogen oxides (NOx), carbon monoxide (CO), and particulate matter, is essential for ensuring compliance with environmental regulations and minimizing the generator's impact on air quality. By optimizing combustion processes and fuel efficiency, operators can reduce emissions and improve environmental performance.
5. Power Output: Monitoring the power output of a diesel generator allows operators to assess its efficiency in converting fuel into electricity. By comparing the actual power output with the rated capacity, operators can identify performance losses and take corrective actions to improve efficiency.
Monitoring Technologies
Several technologies are available for monitoring the performance and efficiency of diesel generators. These technologies range from basic instrumentation to advanced monitoring systems that provide real-time data analytics and remote monitoring capabilities. Some of the common monitoring technologies used for diesel generators include:
1. Engine Management Systems: Engine management systems are onboard computers that monitor and control the operation of diesel engines. These systems collect data on key parameters, such as fuel consumption, temperature, pressure, and emissions, and provide insights into the engine's performance. Engine management systems can also generate alerts for abnormal conditions and facilitate preventive maintenance.
2. Remote Monitoring Systems: Remote monitoring systems enable operators to track the performance of diesel generators from a central location or through a web-based interface. These systems use sensors and communication technologies to transmit real-time data on fuel consumption, power output, temperature, and other parameters. Remote monitoring systems provide operators with visibility into generator performance and enable proactive maintenance and troubleshooting.
3. Data Logging Devices: Data logging devices are portable instruments that record data from sensors attached to diesel generators. These devices can capture information on fuel consumption, load profile, temperature, and other parameters for later analysis. Data logging devices are useful for conducting periodic efficiency audits and identifying trends in generator performance over time.
4. Energy Management Software: Energy management software is a comprehensive tool for monitoring and optimizing the performance of diesel generators within a broader energy management system. These software solutions integrate data from multiple sources, such as generators, grid power, and energy storage systems, to provide a holistic view of energy consumption and efficiency. Energy management software can help operators optimize load scheduling, minimize peak demand charges, and improve overall energy efficiency.
Best Practices for Optimizing Generator Performance
To maximize the efficiency of diesel generators and ensure reliable operation, operators should follow best practices for monitoring and maintenance. Some of the key best practices include:
1. Regular Inspections: Conducting routine inspections of diesel generators is essential for identifying potential issues before they escalate. Inspections should include checks of fuel lines, filters, coolant levels, and electrical connections to ensure proper operation.
2. Scheduled Maintenance: Adhering to a scheduled maintenance program is critical for extending the lifespan of diesel generators and preventing unexpected failures. Regular maintenance tasks, such as oil changes, filter replacements, and engine tune-ups, should be performed according to the manufacturer's recommendations.
3. Fuel Quality Management: Ensuring the quality of fuel used in diesel generators is essential for optimal performance and efficiency. Contaminated or degraded https://www.lkpowerplant.com/60kw-150kw/ can lead to engine problems and reduced efficiency. Operators should monitor fuel quality regularly and implement filtration and treatment measures as needed.
4. Load Management: Optimizing the load profile of diesel generators is key to maximizing efficiency and minimizing fuel consumption. Operators should match the generator's capacity to the actual load requirements and avoid running the generator at low or high loads for extended periods.
5. Performance Monitoring: Implementing a comprehensive performance monitoring system for diesel generators is crucial for tracking key parameters and detecting anomalies. Operators should use a combination of instrumentation, remote monitoring, and data analysis tools to monitor fuel consumption, emissions, temperature, and other performance indicators.
Conclusion
Efficiency monitoring of diesel generators is essential for optimizing performance, reducing costs, and ensuring reliable operation. By tracking key parameters, such as fuel consumption, load profile, temperature, and emissions, operators can identify inefficiencies and take corrective actions to improve efficiency. Monitoring technologies, such as engine management systems, remote monitoring systems, data logging devices, and energy management software, provide operators with the tools to track generator performance and make informed decisions. By following best practices for maintenance, fuel quality management, load management, and performance monitoring, operators can maximize the efficiency of diesel generators and achieve long-term benefits in terms of cost savings, environmental compliance, and equipment longevity.
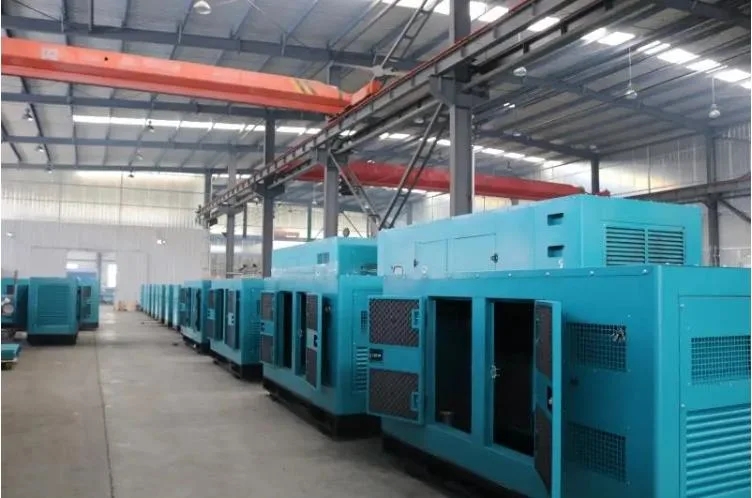